Scotland’s Cost Effective Construction? Modular Housing V’s Modular Scaffolding
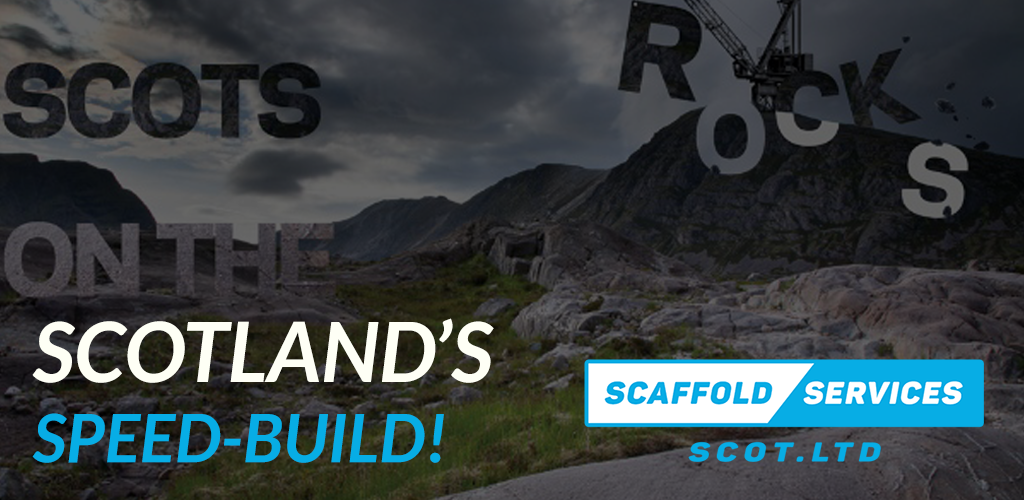
As Scotland becomes reshaped, in the many unfolding ways, construction has seriously soared through new initiatives such as; The Scottish Hub Programme.
The Scottish Government has many new initiatives, one being; to produce 25k newly built homes per annum by 2020. The optimistic target may in fact, be just that. Given, the most homes ever built in a year within Scotland has only ever reached 15k.
Scotland’s Speed Build – Acceleration
In order to reach the new targets delivered by the Scottish Government, Scotland is looking at all possible options to permit speed in construction, safety of supply and of course, cost efficiency.
The question is, how does Scotland meet the 25k new homes per year target, when 15k has been the highest home build target ever reached in a 12-month period?
Cost Effective, FAST Construction
The two options for construction are traditional, using scaffolding to permit access for contractors to build, or prefabricated, modular construction, ready to assemble on arrival.
let’s take a look at how traditional homes are constructed, “stick frame” fabrication – as known by many within the industry. Meaning, traditional timber / steel frames with building works starting on the lower levels first, outside the frame, working up and in as development progresses onto completion.
Modular Scaffolding – Stick Built Homes
Traditional “stick built” homes are constructed by contractors, each having their own area of expertise, brought in as and when each stage is complete and ready for next team of professionals, to complete their own contracted part.
Pros
- This type of construction, does bode for better homes, better quality and longevity.
- Costs in comparison can be cheaper with the correct contractors and suppliers in place
- Adaptations and modifications can be made as and when required, in response to any project changes or circumstances – as they happen
- Traditional construction can be cost saving in comparison to modular housing – on materials
- Customisation flexibility, as and when required is easy to implement with traditionally built homes
- Energy efficiency is built into the initial design
Cons
- Building in the traditional way, using modular scaffolding for access and construction, can be timely
- Labour can be costly should projects run over target
- Scaffolding hire can be costly should projects run over target
- Many suppliers, builders and tradesman all relying on each other and materials getting to where then need to be on time

Modular Homes – Prefabricated Construction
Modular homes, in recent years have been dubbed “Pop-Up” Housing, was once seen as a thing of the 70’s brought in for low cost, low quality accommodation. Over the past very recent years, we have seen the slow but sure return of Modular homes (Pop-up Housing).
It’s reassuring to say, the quality of the new generation of Modular Housing has improved significantly.
Modular homes are prefabricated, constructed within a factory setting, on an assembly line, providing in essence – a one-stop-shop.
Pros
- Speed of construction compared to “stick built” homes is far greater
- One supplier / manufacturer, delivering from the same place, cuts time compared to “stick built” methods which require multiple suppliers and deliveries all hopefullysyncing up and delivered to site, on time
- Modular homes can be up to 15-20% cheaper to buy than traditional homes
- Modular homes are cheaper to build, due to speed of construction
- Energy efficiency can at times be greater, if costs are not cut on tight seams and state of the art windows, LED lighting and efficient solar heating systems
Cons
- For those looking to buy, be careful as the selling value of a modular home is far less than the same sized or functioning “stick-built” home
- Lack of customisation, due to prefabricated sections modular homes are built in a variety of configurations, flexibility is next to nil once delivered to site, it has to be erected exactly as it was fabricated in the factory.
- Mortgages for stick built homes are muddy – literally. Not easy to get without a hefty deposit. The builder needs paid upfront, added with regular payments as development progresses, requiring a construction loan, that is changed to a mortgage only once construction is complete, and the development deemed a residential property
- Costs are heavy on materials and paid upfront – before works have began

The End of Scottish Scaffolding in Construction?
Does the new plans, targets and initiatives the Scottish Government has, mean the end of Scottish scaffolding in construction?
The targets set, are mighty – a way to meet these targets needs found, and fast.
However, that does not mean the end of scaffolding in construction.
Should the route be chosen that all new housing brought in by the Scottish Governmentis prefabricated, modular housing. There will still and always be, a need and requirement for scaffolding and access equipment.
Additional to the speedy construction benefits the “pop-up” housing offers, you can’t take away the fact scaffolding provides those working at height, safety, stability and protection, alongside those in proximity safety from debris and falling materials.
Prefabricated housing cannot offer a 100% complete solution.
It significantly cuts construction time however, sectors will still require height for hire or sale in order to complete works such as roof works, brick works and various other finishing and maintenance works.
In Summary
It’s suffice to say, both options have their own pros and cons.
If speed of construction is the only sole objective, then modular housing and its prefabricated nature is by far the best route.
Scaffolding will always be an essential to permit work at height, regardless of modular builds, tradesman still need access to inspect, finish and complete – any type of construction.
If you’d like more details on any of the system scaffolding, scaffolding supplies and access equipment available from PHS Hire and Sales, contact us on – 01698 535 699, email us at – INFO@PHS.LTD or visit us – PHS.LTD